The Complete Guide to Nylon 6 Filament Yarn: Properties, Applications, and Benefits
11/16/20248 min read
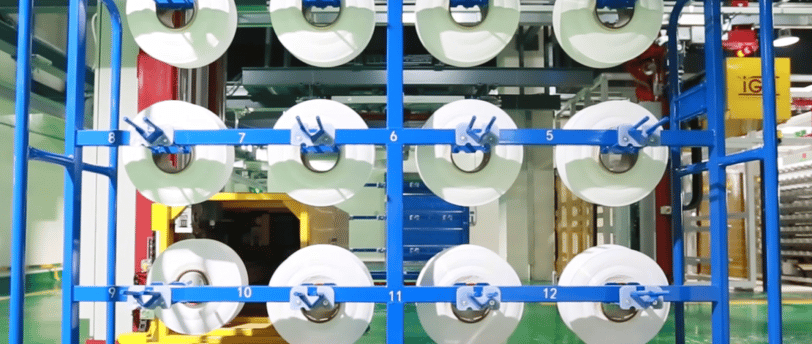
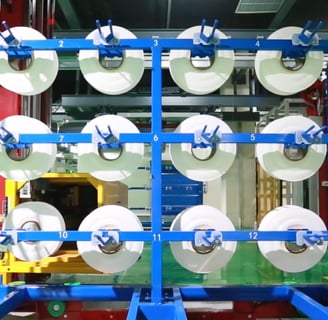
Introduction to Nylon 6 Filament Yarn
Nylon 6 filament yarn, a member of the nylon family, is synthesized from a chemical compound known as caprolactam. This process involves a unique polymerization reaction, resulting in a versatile and durable synthetic fiber. The inception of nylon production traces back to the 1930s when it was first introduced as a replacement for silk in various applications. Its pioneering development by Wallace Carothers at DuPont marked a significant advancement in textile technology, eventually leading to the introduction of nylon 6, which differs from nylon 66 in both its chemical structure and physical characteristics.
Nylon 6 exhibits a singular polymer chain structure, which enables it to have different properties compared to its counterpart, nylon 66. The distinction between these two forms of nylon primarily lies in their molecular arrangement; nylon 6 consists of a single amide link per polymer chain, while nylon 66 comprises two. As a result, nylon 6 filament yarn tends to possess greater elasticity, resilience, and overall softness, making it a preferred choice for various applications in the textile industry.
The manufacturing process of nylon 6 filament yarn involves several steps, including synthesis, spinning, and texturing. Initially, caprolactam is polymerized into a long chain of nylon 6, which is then melted and extruded through a spinneret to create fine filaments. These filaments can be further processed through a method known as texturizing, which enhances their bulkiness and stretchability. This careful manufacturing process results in yarns that are strong, lightweight, and resistant to abrasion, making them ideal for a wide range of applications in fashion, textile, and industrial sectors.
Key Properties of Nylon 6 Filament Yarn
Nylon 6 filament yarn is renowned for its remarkable properties, making it a preferred choice in various applications. One of the primary characteristics of nylon 6 is its exceptional strength. This filament yarn offers high tensile strength, which means it can withstand significant loads without breaking. Compared to natural fibers and some other synthetic yarns, nylon 6 demonstrates superior strength attributes, allowing it to perform admirably in demanding conditions.
Durability is another significant property of nylon 6 filament yarn. It is resistant to degradation caused by environmental factors such as UV rays and moisture, which enhances its longevity. This resilience is particularly advantageous in outdoor applications, such as upholstery and outdoor gear, where exposure to harsh conditions is a common concern.
Elasticity is a crucial aspect of nylon 6, contributing to its ability to retain shape and resist deformation under stress. This elasticity ensures that products made with nylon 6 filament yarn can return to their original form after stretching or compressing, making it invaluable in applications such as clothing and stretch fabrics.
Moisture-wicking ability is another noteworthy feature of nylon 6. Unlike some materials that retain moisture, nylon 6 effectively pulls moisture away from the skin, facilitating quick evaporation. This property makes it an excellent choice for performance wear and activewear, where comfort and temperature regulation are essential.
Resistance to abrasion and chemicals further sets nylon 6 apart from other yarn types. It can endure friction and contact with various chemicals without significant deterioration, making it suitable for industrial applications as well as consumer products. The combination of these properties allows nylon 6 filament yarn to perform effectively in a wide range of products, from textiles to automotive components, thereby reinforcing its status as a versatile material in the fabric industry.
Applications of Nylon 6 Filament Yarn
Nylon 6 filament yarn serves as a cornerstone material across various industries, owing to its unique properties such as strength, elasticity, and resistance to abrasion and chemicals. Its diverse applications reflect its versatility, making it a preferred choice in both consumer products and industrial sectors.
In the textile industry, nylon 6 filament yarn is widely used in the production of clothing, activewear, and other fabric goods. Items such as swimwear, hosiery, and lingerie benefit from the yarn's flexibility and moisture-wicking properties, providing comfort and performance. Furthermore, this yarn is often blended with natural fibers to enhance durability and improve the overall texture of fabrics, which is particularly evident in sports and outdoor clothing.
The automotive sector also leverages the attributes of nylon 6 filament yarn, utilizing it in components like seat belts, airbags, and interior fabrics. The yarn's resistance to wear and tear makes it an excellent choice for safety-critical applications, ensuring longevity and reliability. Additionally, it is used in under-the-hood parts and electrical systems due to its thermal stability, aiding manufacturers in meeting stringent safety standards.
In the medical field, nylon 6 filament yarn is employed in various applications including sutures and medical garments. Its biocompatibility, strength, and ability to be sterilized make it ideal for these uses, contributing to improved patient outcomes. Moreover, the yarn is often found in the production of devices such as braces and supports, which require durable materials that can withstand rigorous use.
Finally, in the realm of home goods, nylon 6 filament yarn finds its way into items like carpets, upholstery, and bags. Its resistance to stains and easy maintenance ensures that products maintain their quality over time, making it a favored choice for consumers. This wide range of applications highlights not just the efficacy of nylon 6 filament yarn, but also its essential role in enhancing the functionality and aesthetic of various products across different domains.
Advantages of Using Nylon 6 Filament Yarn
Nylon 6 filament yarn presents numerous advantages that make it a preferred choice for both manufacturers and consumers. One key benefit is its cost-effectiveness. Nylon 6 is generally more affordable to produce compared to other synthetic fibers, resulting in lower production costs for end products. This economical aspect draws manufacturers to employ nylon 6 filament yarn in diverse applications ranging from textiles to industrial products.
The lightweight nature of nylon 6 filament yarn further enhances its appeal. Its reduced weight makes it ideal for applications where minimizing weight is crucial, such as in apparel and outdoor gear. This property not only improves comfort but also increases ease of use, resulting in enhanced performance characteristics in various products. Moreover, nylon 6 has excellent tensile strength, which contributes to its durability and longevity in products exposed to stress and wear.
Additionally, nylon 6 filament yarn is known for its ease of dyeing, allowing for vibrant color application and uniformity. This feature is particularly valuable in the fashion industry, where fabric aesthetics play a significant role in consumer choices. The ability to achieve a wide range of colors and shades quickly and efficiently gives manufacturers flexibility in design, thus enhancing market competitiveness.
Nylon 6 also exhibits compatibility with other fibers, enabling the creation of blended yarns. This characteristic allows manufacturers to harness the benefits of multiple materials, optimizing fabric properties such as softness, breathability, and moisture-wicking abilities. Blends can enhance the performance and appeal of textiles, making them suitable for specific uses based on desired attributes.
In terms of environmental impact, while nylon is a synthetic fiber, advancements in the recycling of nylon 6 are making it increasingly sustainable. Efforts to manufacture nylon 6 from renewable resources are being explored, contributing to minimal ecological footprints. As a result, its use is becoming more viable, providing an environmentally responsible alternative to traditional materials.
How to Care for Nylon 6 Filament Products
Nylon 6 filament yarn is well-regarded for its strength, durability, and versatility, making it a popular choice for various applications, ranging from clothing to industrial products. Proper care and maintenance of items made from nylon 6 filament can significantly enhance their lifespan and performance, ensuring they remain in excellent condition over time.
When washing nylon 6 filament products, it is advisable to use a gentle cycle with cold or lukewarm water. High temperatures can compromise the integrity of the fibers, leading to shrinkage or loss of elasticity. It is best to employ a mild detergent, free from bleach or fabric softeners, as harsh chemicals can weaken the fibers and dull the material’s luster. Additionally, avoid overloading the washing machine to allow for proper agitation and rinsing, which helps in removing dirt and grime more effectively.
For drying, air drying is typically the most suitable option for nylon 6 filament items. Lay the product flat on a clean, dry towel or hang it in a shaded area to prevent direct sunlight from causing fading or heat damage. If machine drying is necessary, use a low heat setting, regularly checking the items to prevent overheating.
Storage of nylon 6 filament products is also crucial in maintaining their quality. They should be kept in a cool, dry place, away from excessive moisture and sunlight. When storing garments, it is preferable to fold them instead of hanging to avoid stretching. Additionally, make sure that storage areas are well-ventilated to deter mildew, which can damage nylon fibers.
In summary, knowing how to properly care for and maintain nylon 6 filament yarn products can make a meaningful difference in their longevity and appearance. By following these washing, drying, and storage tips, consumers can keep their nylon items looking new and performing optimally throughout their usage.
Innovations in Nylon 6 Filament Yarn Technology
The production of nylon 6 filament yarn has seen substantial advancements in recent years, driven by both technological innovations and a growing demand for sustainable materials. One key area of development is in the manufacturing techniques used to produce nylon 6 yarn. Traditional methods are continually being refined, leading to improvements in both quality and efficiency. For instance, the introduction of advanced spinning technologies has enabled manufacturers to create finer and stronger yarns, which cater to a broader range of applications. This signifies a notable shift towards high-performance nylon 6 filament yarns that can withstand various stresses, making them suitable for diverse industries such as automotive, textiles, and even aerospace.
Moreover, the emergence of new blends and composites is revolutionizing the functionality of nylon 6 filament yarn. By incorporating other materials or modifying the molecular structure of nylon 6, manufacturers are able to engineer yarns that exhibit unique properties, such as enhanced elasticity, increased strength, and improved resistance to environmental factors. This trend is particularly evident in the production of nylon 6 yarn blended with recycled materials, which not only reduces waste but also lowers the carbon footprint of the end products. These innovations are pivotal as they align with the global push towards eco-friendly manufacturing practices.
The integration of smart technologies is further shaping the future landscape of nylon 6 filament yarn. Advancements such as the Internet of Things (IoT) are enabling real-time monitoring of the production processes, enhancing quality control and minimizing material waste. Additionally, companies are increasingly investing in research and development to explore the potential of bio-based nylon 6 alternatives, a move that reflects a commitment to sustainability while meeting the diverse needs of modern consumers.
Conclusion and Future Outlook for Nylon 6 Filament Yarn
Nylon 6 filament yarn has established itself as a crucial material across multiple sectors due to its unique properties such as flexibility, strength, and resistance to wear and tear. Throughout this guide, we have explored its various applications including textiles, industrial products, automotive components, and electronics. These qualities make it an essential choice for manufacturers aiming to achieve durability while maintaining lightweight characteristics.
As we look towards the future, the market for nylon 6 filament yarn is poised for growth, fueled by several emerging trends. The increasing demand for high-quality, durable materials in fashion and technology sectors indicates a promising expansion for nylon 6. Furthermore, the trend toward sustainability will likely impact production methods; many manufacturers are beginning to explore the use of recycled materials to produce nylon 6 filament yarn. This shift not only addresses environmental concerns but also caters to a growing consumer base that prioritizes sustainability.
Ongoing research in the field is also likely to bring about innovations in nylon 6 filament yarn formulations and production techniques. Improved manufacturing processes, designed to enhance performance while reducing environmental impact, are on the horizon. The development of bio-based nylon alternatives presents another avenue for future exploration, potentially revolutionizing the material's lifecycle.
As the industry adapts to changing market demands and technological advancements, the significance of nylon 6 filament yarn is expected to grow. Its role in shaping industries underlines its importance not just today but also in the times to come. With ongoing research and a focus on sustainable practices, the future of nylon 6 filament yarn appears promising, marking it as a material to watch in the coming years.